Weit auskragendes Vordach für Sportcampus im Olympiapark
Holzbauprojekt im großen MaßstabFür den Neubau des Sportcampus im Münchner Olympiapark werden bis 2023 über 5200 m³ Holz eingesetzt. Schon jetzt kann das spektakuläre Holzdach bestaunt werden, das auf 150 Meter Länge über 18 m auskragt. Die Vorfertigung und Montage der Elemente für das Vordach war eine logistische Herausforderung.
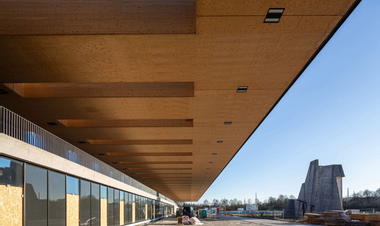
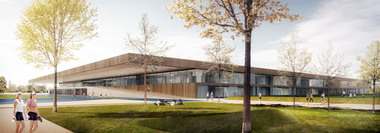
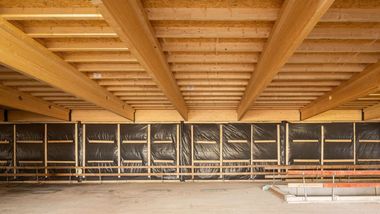
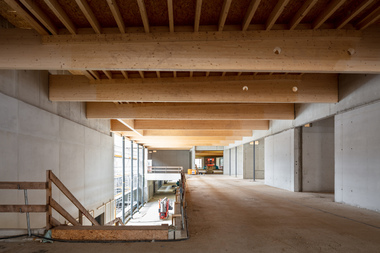
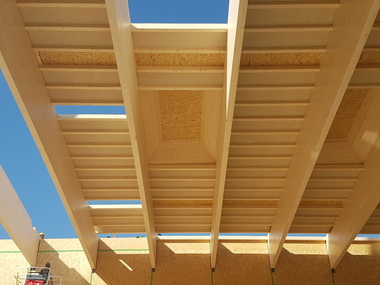
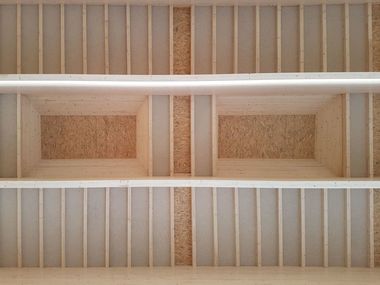
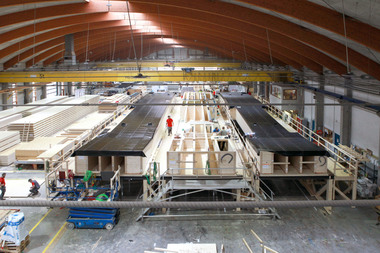
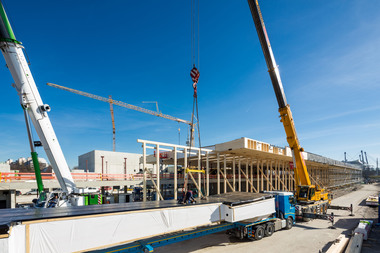
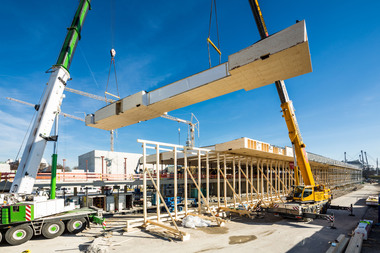
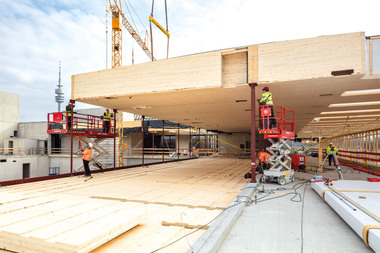
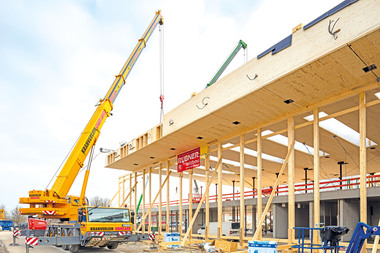
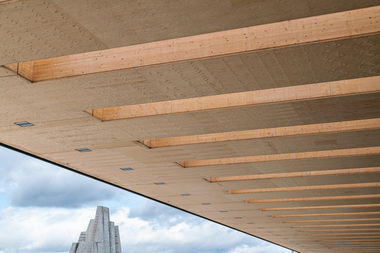
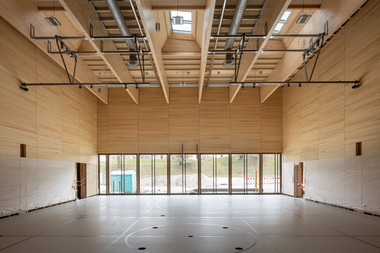
Im denkmalgeschützten Münchner Olympiapark entsteht derzeit der Campus im Olympiapark (CiO) der Technischen Universität München. Gebaut wird er überwiegend aus Holz. Auf gut 180 x 150 m Fläche entstehen je zwei zweigeschossige Hallen- und Bürogebäude mit sechs Innenhöfen. Damit wird der Campus einer der größten Holzbauten Europas, geplant von Dietrich/Untertrifaller Architekten aus Bregenz und den Tragwerksplanern merz kley partner ZT aus Dornbirn. Bis 2023 werden für das Bauprojekt über 5200 m³ Holz verbaut. Auf fast 19 000 m² Nutzfläche entstehen 300 Büros, 14 Sporthallen, 12 Hörsäle, fünf Werkstätten, eine Cafeteria und eine Bibliothek, zudem 15 Diagnostikräume.
Gigantischer Holzbau
Sporthallen, Institutsbereiche und die komplette Dachkonstruktion der Campusanlage werden in Holzbauweise errichtet, die Decken als Hohlkästen oder in Holz-Beton-Verbundbauweise ausgeführt. Nur dort, wo es für Brandschutz oder Statik nötig war, wurde Stahlbeton verwendet – immerhin rund 10 000 m³ mit rund 900 t Stahl. Der Hauptzugang zum Campus liegt im Osten. Vom Olympiapark führt ein Steg in die zentrale Verbindungs- und Erschließungsachse im Obergeschoss. Diese Passage, von den Planern auch „Rue Interieure“ genannt, zieht sich durch das ganze Gebäude. Besucher und Nutzer erhalten hier später Einblicke in alle Hallen, Hörsäle und die verglasten Seminarräume. Nach 180 m öffnet sich das Gebäude mit einem weit auskragenden Vordach. Von hier blickt der Besucher auf das neue Leichtathletikstadion und das gesamte Freigelände. Der verantwortliche Architekt Heiner Walker von Dietrich/Untertrifaller Architekten weist auf die enorme Auskragung des Holzdachs bei gleichzeitig minimaler Höhe hin: „Holz ist mit seinem geringen Gewicht bei hoher Festigkeit das ideale Baumaterial dafür.“ Statiker Gordian Kley hat nachgerechnet: „In Stahl hätten wir etwa 400 t benötigt und es hätte ein riesiges Wärmebrückenproblem gegeben. So haben wir, grob überschlagen, 900 Tonnen CO2 eingespart.“
Bauen im Betrieb
In laufendem Betrieb sind bisher zwei Bauabschnitte abgeschlossen: die beiden neuen Hallengebäude, die Mensa, die Bibliothek und das westliche Vordach. Ebenso die komplette „Rue interieure“, ein Großteil des Untergeschosses und die haustechnischen Anlagen. Rubner Holzbau aus Augsburg war dabei für den Holzbau verantwortlich. „Die Organisation war eine große Herausforderung und alles so zu takten, dass die Baustelle ständig mit Baumaterial versorgt wird“, betont Volker Schreier, Projektleiter bei Rubner Holzbau.
Die neuen Hallen wurden um die alten Hallen herum gebaut. „Ziel war es, die Bauzeiten möglichst kurz zu halten, um den laufenden Betrieb möglichst wenig zu stören“, betont Architekt Walker. „Im Holzbau spart man in der Ausführung sehr viel Zeit“, bekräftigt Gordian Kley, „dafür muss man mehr planen.“ Im dritten Bauabschnitt werden die Bestandshallen abgebrochen und dort die Gebäudeteile mit den Büros errichtet. Abschließend folgen die Außenanlagen mit den Sportflächen.
Schneller mit 3D-Plänen
Rubner Holzbau führte auch die Holzbau- und Werkstattplanung aus – und zwar in 3D. Um die Planung zu dokumentieren, zu prüfen und rechtlich abgesichert zu sein, werden normalerweise 2D Pläne mit Schnitten erzeugt, beschriftet und bemaßt. „Wir haben das am Anfang auch so gemacht, aber dann irgendwann gesagt, das hat so keinen Zweck“, erinnert sich Heiner Walker, „diesen Zwischenschritt wollten wir uns sparen.“ Rubner musste dazu schriftlich bestätigen, dass alle Pläne die sie den Architekten vorlegten, aus den 3D Plänen, aus einer Datenquelle, generiert sind. Die Architekten überprüften dann im Wesentlichen nur das 3D Modell.
Passage mit Holzdach
Die mittige Passage des Gebäudes ist auch die zentrale Rettungsgasse und gilt als Versammlungsstätte. Nach den Brandschutzvorschriften muss ihr Tragwerk bis zur Unterkante Dachkonstruktion brandbeständig (F90) sein. Deshalb ist sie zu einem Großteil aus Stahlbeton gebaut, hat allerdings ein Holzdach. Brettschichtholzträger spannen dabei im Abstand von fünf Metern maximal 30 m weit; dazwischen sind KVH-Pfetten eingebaut. Im Werk wurden die Pfetten auf OSB-Tafeln geschraubt, darüber kam eine Dachabdichtung. Auf der Baustelle wurden die vorgefertigten Elemente auf die Binder gelegt und die überlappenden OSB-Tafeln auf ihnen vernagelt, so dass sie die Dachelemente aussteifen.
Sporthallen mit Sichtoberflächen
Auch für die 14 Sporthallen und eine Kletteranlage wurden die vollständig sichtbar bleibenden Dachflächen weitgehend vorgefertigt. Sie bestehen aus bis zu 30 m langen und maximal 1,8 m hohen Satteldachbindern mit geradem Untergurt im Gebäuderaster von 2,50 m. Rechtwinklig über den Bindern liegen Dachelemente aus kleinen Pfetten und aussteifenden OSB-Tafeln sowie Holzwolle-Leichtbauplatten als Akustikelemente. Einzelne Felder öffnen sich über konische Aufsätze aus Dreischichtplatten zu Oberlichtern. Bei der Montage wurden Felder als Passfelder vorerst offengelassen. Die Wandelemente für die Ständerwände wurden in Großtafeln vorgefertigt, inklusive der Dachstützen. Sie sind bis zu 1,2 t schwer. Mit OSB-Platten innen und DWD-Platten außen ist der Wandaufbau dampfdiffusionsfähig.
Enorm auskragendes Vordach aus Holz
Spektakulär kragt das Vordach im Süden 18,3 m weit über die Achse der Glasfassade aus und überdacht auf einer Länge von 153 m eine spätere Laufbahn. Im Wettbewerbsentwurf sollte das Dach sogar 22 m auskragen, aber aus Kostengründen wurde es gekürzt. Auch so kostet es noch zirka 2000 Euro/m², rechnet Architekt Heiner Walker vor und gibt zu: „Für ein Vordach ist das viel Geld. Aber gleichzeitig bietet es diese Boxengasse, die uns so wichtig war.“
Aufgebaut ist das Vordach aus 40 Hohlkastenelementen mit 28 m Länge, 3,75 m Breite und nur 1,6 m Konstruktionshöhe. Die Elemente bestehen aus schlanken Längsrippen, überbreiten Querträgern in BSH und Platten aus Furnierschichtholz (Fichten-/Tannenholz) als Beplankung. Die Platten mussten möglichst lang sein, zum Einsatz kamen 600 m³ „Kerto“-Platten in bis zu 20 m Länge.
Neue Dimension der Vorfertigung
Die Anschlüsse der Längsrippen an die Querträger erfolgten mechanisch über Schrauben und Rillennägel in Verbindung mit gekanteten Blechen. Die großen Auflagerkräfte in die Stahlstützen werden über Stahlplatten und lange, querdruckverstärkende Vollgewindeschrauben übertragen. Auf Rippen und Träger wurden die bis zu 20 x 2,50 m und 1,5 t schweren Platten aufgelegt und über eine Schraubpressklebung verbunden. Als Leim wurde ein fugenfüllender Resorcinharzleim mit dem Zahnspachtel aufgetragen. Das besondere an diesem Leim ist, dass er fugenfüllend und sehr witterungsbeständig ist, dazu muss er aber auch mit dem Zahnspachtel aufgetragen werden. Damit die Platten belastbar verklebt werden konnten, wurden sie von 52 auf 49 mm Dicke gehobelt. Noch im Werk erhielten die Elemente eine Abdichtung, alle elektrischen Leitungen und die Entwässerungsleitungen, die hinter den Leibungsbrettern der Oberlichter liegen, wurden verlegt. Im hinteren Drittel sind alle Kammern der Kastenelemente über Durchbrüche gekoppelt, um das Klima innerhalb der Kästen auszugleichen und eine Überwachung zu ermöglichen. Durch Wartungsöffnungen in der Untersicht bleiben sie zugänglich für Kontrollen.
Montage im Tandembetrieb
Mit Spezialtiefladern wurden die 19 t schweren Elemente im Werk unterfahren und auf die Baustelle gebracht. Dort setzten sie zwei Kräne im Tandembetrieb auf. Lange, dicke Vollgewindestangen versteifen die Dachelemente als Zugstangen zum Vordach. Bei dem Tragwerk der Elemente war die große Herausforderung die Verformung unter Last. „Wir haben hier riesige Kräfte“, erklärt Statiker Kley, „oberstes Gebot war, dass es niemals so weit kommt, dass das Wasser nach hinten wegläuft.“ Deshalb wurden die Hohlkästen mit einer Überhöhung von 20 cm am äußersten Ende montiert. In der Bauphase war ihre äußere Kante durch einen Bock unterstützt. Als der Bock abschnittsweise herausgenommen wurde, senkte sich das Dach wie berechnet um 7 cm.
Akustik außerhalb der Norm
Die vorgefertigten Decken der Sporthallen erhielten Holzwolle-Leichtbauplatten als Akustikelemente. Für eine hohe Sprachverständlichkeit, wie sie für Lehrveranstaltungen nötig ist, war ursprünglich vorgesehen, die Wandelemente über ihre gesamte Höhe zu lochen und mit einem wirksamen Akustikvlies zu hinterlegen. Aus Kostengründen wurde dieser Aufbau auf den unteren Bereich reduziert. Doch ein Akustiker stellte fest, dass die neue Norm für Hörsamkeit in Räumen so nicht eingehalten wurde. „Überzogene Akustikforderungen“, ärgert sich Heiner Walker und ergänzt: „Da ist es gut, wenn man die Dinge, die einem von der Normung vorgesetzt werden, hinterfragen kann. Wir haben gesagt, das funktioniert.“ Und er konnte den Bauherren durch den Besuch einer ähnlichen, schon realisierten Halle überzeugen. „Wir bauen hier außerhalb der Norm mit dem Segen des Bauherrn und zugunsten von einem wirtschaftlich umsetzbaren Projekt“, fasst er zusammen. Die deutschen Normen seien nicht auf den Holzbau ausgelegt, meint Walker. „Bei so einem Projekt braucht man außerdem einen guten Brandschutz, der auch Ausnahmen formulieren kann“, ergänzt der Architekt. So gab es etwa keine Brandschutzklappe für die Lüftungsleitungen, die für den Einbau in den Holzständerwänden zugelassen waren. Abhilfe schaffte eine Zulassung im Einzelfall.
Kunst der Wasserführung
Durch die Hallenbinder sind die wichtigsten Gefällelagen auf dem Dach bereits hergestellt. „Das ist wesentlich geschickter, als wenn man versucht, das mit einer Gefälledämmung zu machen“, bekräftigt Walker. Um das Wasser mit Dampfsperre und Notabdichtung schon in der Bauphase in die richtige Richtung zu leiten, wurden die Stöße der Abdichtung sofort heiß verklebt. Später ergänzten die Dachdecker an den aufgehenden Längswänden schmale Keile mit Gegengefälle und banden sie in die Abdichtung mit ein, um das Wasser vom Holz weg zu den Abläufen zu führen. Der Dachaufbau besteht nun, von innen nach außen, aus einer Bitumen-Dampfsperre, einer druckfesten Steinwolldämmung, darüber folgt wieder eine Bitumenabdichtung und abschließend ein Gründach.
Wenn das große Holzbauprojekt des Campus im Olympiapark 2023 vollendet wird, werden die Gebäude und die neuen Außenanlagen von 2400 Studenten und Studentinnen sowie etwa 17 000 Sportaktiven pro Semester genutzt.
AutorAchim Pilz ist Architekt, Baubiologe (IBN), Buchautor, freier Journalist und Chefredakteur des Baubiologie Magazins.
Bautafel (Auswahl)
Projekt Campus im Olympiapark der Technischen Universität München
Auftraggeber Staatliches Bauamt München
Architektur Dietrich | Untertrifaller Architekten ZT GmbH, Bregenz (AT), www.dietrich.untertrifaller.com
Tragwerksplanung merz kley partner ZT, Dornbirn (AT), www.mkp-ing.com
Holzbau Rubner Holzbau, 86167 Augsburg, www.rubner.com
Fertigstellung 2023
Gesamtkosten etwa 163 Mio. Euro